AGC's Carrier Glass Technology with Bonding Layer
- Flexible Sensor Device
- Thinner Sensor Device
- 1. Easy Handling of Ultra-Thin Glass (UTG)
- 2. Mechanical Lift-Off (MLO)
- What is MLO?
- Comparison with Laser Lift-Off (LLO):
- Advantages of AGC's MLO:
- 3. High heat resistance of Bonding Layer
- 4. Available in Large Sizes
- What Are the Differences Between Carrier Glass Technology with Bonding Layer and Standard Carrier Glass?
- How to Order Ultra-Thin Glass and Carrier Glass?
01/What is "AGC's Carrier Glass Technology with Bonding Layer”?
AGC's Carrier Glass Technology is a groundbreaking solution for handling and processing ultra-thin glass (UTG). It overcomes a key challenge associated with UTG's incredible thinness and flexibility – its delicate nature makes it difficult to integrate into existing manufacturing processes without damaging the material.
This technology's core is a lamination process that bonds an ultra-thin layer of UTG, less than 0.1 mm thick, onto a sturdier carrier glass. A specialized bonding layer is strategically placed between these two glass components, creating a robust and stable composite material. This composite substrate retains the exceptional properties of UTG, such as transparency, heat resistance, and electrical insulation, while significantly enhancing its manageability.
Integrating AGC's Carrier Glass Technology into the manufacturing process is relatively straightforward. The carrier glass with the bonded UTG is supplied to the customer, who then incorporates it into their product development cycle. Once the desired sensor or circuit is formed on the UTG layer, the carrier glass can be removed through a process known as Mechanical Lift Off (MLO). It leaves behind the patterned UTG that is ready for integration into the final product.
The process can be summarized as follows:
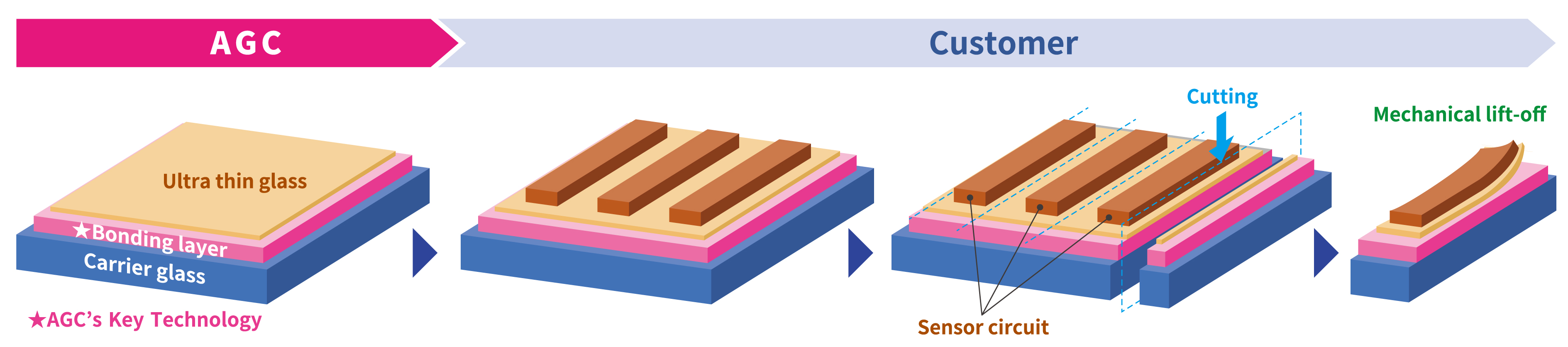
1. AGC Production: Ultra-thin glass is bonded to carrier glass using a specialized bonding layer.
2. Customer Integration: The laminated glass substrate is delivered to the customer.
3. Sensor/Circuit Formation: The customer forms the desired sensor or circuit on the ultra-thin glass layer.
4. MLO Process: The carrier glass is removed through mechanical lift-off, leaving the patterned ultra-thin glass behind.
By providing a reliable and efficient method for handling UTG, AGC's Carrier Glass Technology empowers manufacturers to unlock the full potential of this remarkable material in a wide range of applications, from flexible sensors.
Other AGC's Carrier Glass Technology

Glass substrate for semiconductor packaging
Unlike AGC's Carrier Glass Technology with Bonding Layer, which focuses on handling delicate ultra-thin glass, this product emphasizes high flatness and smoothness, critical for the precision of semiconductor packaging. Supporting various wafer sizes (such as φ300 mm) and panel sizes, AGC’s glass substrates ensure reliable performance in processes requiring high-quality carrier glass, including those with special features like notches, serial numbering, and ID marking.
02/Applications
AGC's carrier glass technology holds immense potential across various industries, primarily due to its ability to enhance the handling and processing of ultra-thin glass (UTG). Two key application areas stand out:
Flexible Sensor Device
One of the most promising applications is flexible sensor devices. The combination of UTG's flexibility and the protective properties of the carrier glass create an ideal foundation for developing innovative sensors that can be seamlessly integrated into curved or flexible surfaces. It opens up possibilities for wearable technology, smart textiles, and human-machine interfaces.
Thinner Sensor Device
Another significant application lies in the creation of thinner sensor devices. The ultra-thin glass substrate, protected by the carrier glass, enables the development of sensors with reduced thickness without compromising performance. It is crucial for applications where device size and weight are critical, such as mobile devices, medical implants, and automotive electronics.
03/Features
AGC's Carrier Glass Technology incorporates several key features contributing to its effectiveness in handling and processing ultra-thin glass (UTG).
1. Easy Handling of Ultra-Thin Glass (UTG)
One of this technology's primary advantages is its ability to simplify the handling of UTG. AGC has transformed a highly fragile material into a more manageable substrate by laminating the delicate UTG onto a thicker carrier glass.
This innovation eliminates the need for specialized handling equipment and reduces the risk of damage during transportation and manufacturing processes. Consequently, manufacturers can streamline operations, reduce production costs, and increase efficiency. This enhanced handling capability is a cornerstone of AGC's Carrier Glass Technology, making it a valuable asset for industries working with ultra-thin glass.
2. Mechanical Lift-Off (MLO)
What is MLO?
Mechanical Lift-Off (MLO) is a process used to separate an ultra-thin layer of UTG (Ultra-Thin Glass) from its carrier glass through mechanical (or physical) means. This method involves the application of a mechanical force to peel away the ultra-thin layer from the sturdier carrier glass, preserving the integrity of the delicate UTG.
Comparison with Laser Lift-Off (LLO):
While MLO uses mechanical force for separation, Laser Lift-Off (LLO) is another method that relies on laser energy to achieve the same result. However, LLO has significant drawbacks, including high initial and running costs. Additionally, LLO poses quality issues, such as the potential to damage the delicate devices during the separation process, making it a less favorable option in certain applications.
Advantages of AGC's MLO:
One of the challenges with MLO is that if the separation force is too strong, there is a risk of damaging the ultra-thin layer or the device. AGC's lamination process addresses this by enabling separation with a low separation force, significantly reducing the risk of damage to the UTG or the associated devices. This low-force separation makes AGC's MLO process particularly advantageous for applications requiring high precision and the preservation of delicate materials.
3. High heat resistance of Bonding Layer
A critical component of AGC's Carrier Glass Technology is the bonding layer, which exhibits exceptional heat resistance and can endure temperatures of approximately 400°C. This thermal resilience is paramount for the technology's efficacy. Numerous manufacturing processes, such as annealing, tempering, and certain coating applications, necessitate exposure to elevated temperatures.
The bonding layer's ability to withstand such conditions ensures the integrity of the laminated substrate, preventing delamination or degradation of the ultra-thin glass. Consequently, AGC's Carrier Glass Technology offers manufacturers a reliable and durable solution that can seamlessly integrate into existing production lines without compromising product quality or yield.
4. Available in Large Sizes
AGC offers large-sized carrier glass technology using large-format glass produced by the float process, to meet the growing demand for large-scale applications and improve process efficiency through large substrates. This capability enables manufacturers to process larger sheets of UTG without compromising quality or efficiency.
By eliminating the constraints of smaller substrate sizes, AGC empowers manufacturers to explore new design possibilities and cater to the growing market for larger-scale devices. This scalability is a testament to AGC's commitment to providing comprehensive solutions that meet the evolving needs of the industry.
04/FAQs
AGC's Carrier Glass Technology has introduced a novel approach to handling and processing ultra-thin glass. We've compiled a list of frequently asked questions to address common inquiries and provide further clarification.
What Are the Differences Between Carrier Glass Technology with Bonding Layer and Standard Carrier Glass?
While both this glass carrier technology and standard carrier glass wafers are designed to support other materials, they serve distinct purposes in different industries.
Standard carrier glass wafers are primarily used in the semiconductor industry as temporary substrates for handling and processing delicate semiconductor wafers during manufacturing. These wafers are engineered to endure the demanding conditions of semiconductor fabrication, such as high temperatures and chemical etching.
In contrast, this glass carrier technology is specifically developed to support and protect ultra-thin glass (UTG) in applications such as sensors and other devices. It is optimized for the handling and processing of UTG while preserving its fragile properties. Although both types of carrier glass share the fundamental purpose of providing support, their specific characteristics, manufacturing processes, and target applications differ significantly.
How to Order Ultra-Thin Glass and Carrier Glass?
AGC provides a convenient solution by offering ultra-thin glass and carrier glass as a combined product. This approach simplifies the ordering process for customers, as they no longer need to source these components separately. Additionally, AGC can supply the bonding layer, realizing optimal adhesion between the ultra-thin glass and carrier glass. This integrated offering highlights AGC's dedication to delivering comprehensive solutions tailored to customer needs.
05/Contact Us
Ready to streamline your manufacturing process and explore the benefits of ultra-thin glass? Contact us today to learn how AGC’s Carrier Glass Technology can enhance your product development, improve handling efficiency, and empower your innovative designs.
Contact us today to learn more
about AGC's Carrier Glass