Flat Glass Manufacturing Process
- Float glass process
- 1.Batching of raw material
- 2.Melting of raw materials in the furnace
- 3.Drawing the molten glass onto the tin bath
- 4.Cooling of the molten glass in the annealing lehr
- 5.Quality checks, automatic cutting, and storage
- Float Glass Process Video
- Oversized Float Glass Manufacturing Video
- Fusion glass process
- 1.Melting
- 2.Refining
- 3.Forming
- 4.Annealing
- 5.Cutting
- Sand
- Soda ash (sodium carbonate)
- Limestone (calcium carbonate)
- Waste recycled glass
- Additives
- Is glass solid or liquid?
- How was glass made historically?
01/Flat Glass Manufacturing Process: Float & Fusion Process Explained
Flat glass is made with sand, recycled glass, or a combination of both. The sand or the recycled glass is melted, typically with soda ash, so the melting point is lowered. Lowering the melting point improves the efficiency of the flat glass manufacturing process because it means that less heat is required to melt the sand. While the sand is being melted, other additives can be added alongside the soda ash.
For example, these could be additives that change the color of glass, increase its refractive index, or enhance heat resistance. The sand is typically melted in a metal container placed inside a furnace. Inside the furnace, the sand goes from a solid state to a liquid state. This liquid state enables the atoms to move around more freely.
Therefore, the arrangement of the atoms will change when it cools, and this allows the glass to form as an amorphous solid. Once the sand is fully melted, it’s removed from the furnace to cool. There are different cooling methods for flat glass, depending on its application. However, all flat glass must be shaped before it cools. As the glass cools, it becomes more viscous (meaning that the consistency is more sticky). Because of this, it’s easier to mold into a shape.
Float glass process
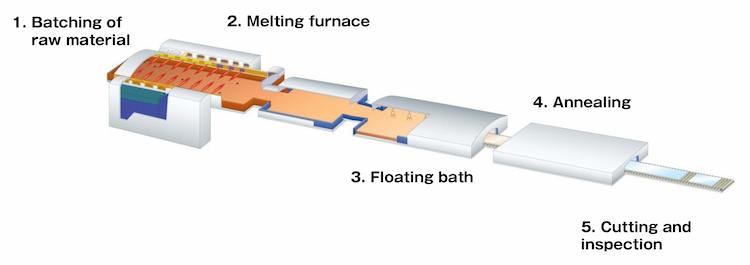
The most common method for creating flat glass is the float glass process. Float glass is made by heating raw materials—silica sand, limestone, soda ash, and magnesium in a furnace. When melted, it’s then spread out over a sizable bed of molten tin. As it moves along rollers in the annealing oven during a controlled cooling process, this mixture slowly solidifies over the molten tin. From this point, a single, continuous smooth ribbon of glass emerges.
1.Batching of raw material
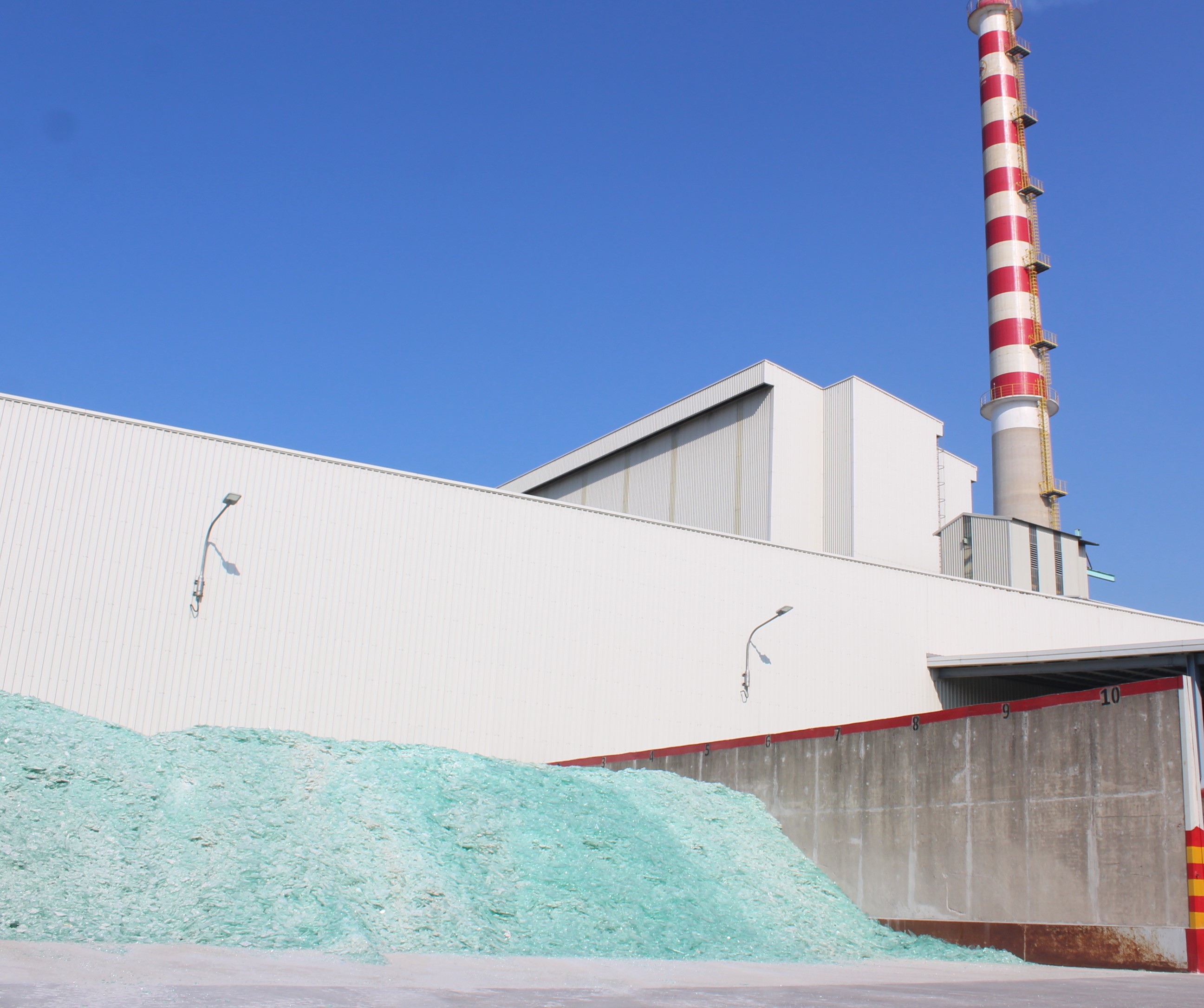
The batching of raw materials varies for different glass. Therefore, float glass requires a specific mixture of raw materials.
The main components of float glass (soda-lime glass) are:
- Silica sand (73%)
- Soda ash (13%)
- Calcium oxide (9%)
- Magnesium (4%)
- Cullet (waste glass)
2.Melting of raw materials in the furnace
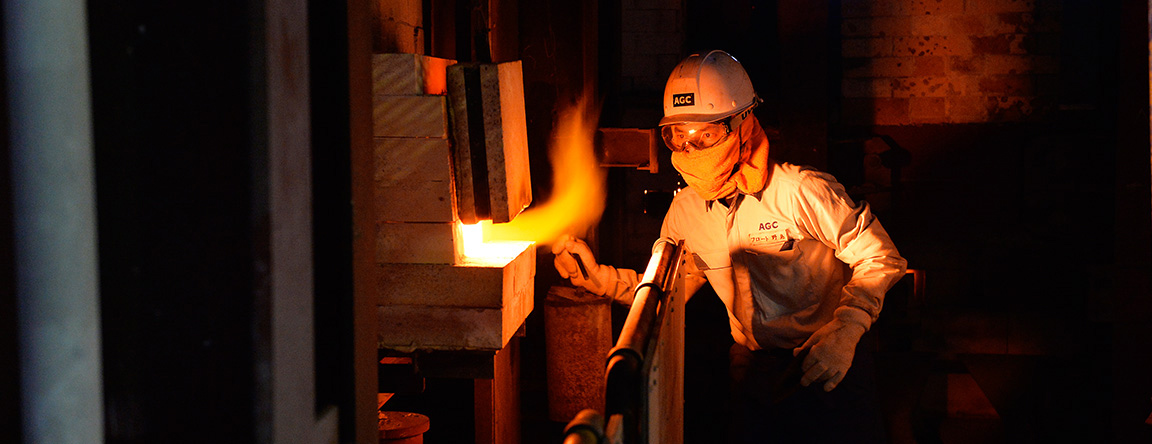
The raw materials are combined in a batch process and then fed into a furnace where they are heated to about 2,732 °F along with cullet (waste glass). Most float glass furnaces can hold about 1,200 tons of glass.
3.Drawing the molten glass onto the tin bath
The melted glass is poured into a bath filled with molten tin. This process takes the molten glass from a delivery canal. A gate known as a tweel regulates the amount of glass that can be poured onto the molten tin. Tin has a high specific gravity, is cohesive, and is immiscible with molten glass, making it an ideal material for the float glass process.
4.Cooling of the molten glass in the annealing lehr
An annealing lehr oven is a lengthy furnace with a temperature gradient. It’s used to anneal (slowly cool) floating glass transported through the gradient on rollers or a conveyor belt. As a result, the glass will be stronger after annealing, with fewer internal stresses and a lower risk of breaking.
5. Quality checks, automatic cutting, and storage
Once the glass has cooled, it will be checked for any imperfections. It can also be cut as required and is stored carefully since large sheets of glass require extra care.
Float Glass Process Video
Oversized Float Glass Manufacturing Video
Fusion glass process
The fusion glass process is another method of making flat glass. However, instead of suspending the melted glass in molten tin, it’s instead suspended in the air.
1.Melting
The process starts by melting the raw materials—silica sand, soda ash, and any required additives.
2.Refining
From here, the melted materials are homogenized (made uniform) before proceeding to the next stage.
3.Forming
The glass is then discharged from the furnace into an isopipe. An isopipe is a large collection trough with a V-shaped bottom. To control the mixture&’s viscosity and guarantee a consistent flow, the isopipe is carefully heated.
While still attached to the isopipe, a sheet of glass feeds into drawing machinery to lengthen and cool in midair. Key characteristics, like glass thickness, are affected by the precise control of this process.
4.Annealing
Annealing occurs while the glass is still suspended in midair. The temperature is controlled carefully to ensure the glass doesn’t cool too fast.
5. Cutting
After the glass has cooled completely, it’s safe to cut it and store it carefully.
02/What is glass made of?
The primary materials of flat glass are sand, soda ash (sodium carbonate), and limestone (calcium carbonate). But some types of glass will have varying additives to enhance their purpose.
Sand
Sand is a granular material commonly found near beaches, rivers, or deserts. It’s typically defined by size. For example, it’s smaller than gravel but coarser than silt. However, it may also be defined by its composition. It can take thousands of years for sand to form. That’s because it forms when rocks break down and erode. Therefore, the exact composition of sand depends on which substances are present in the rocks. Rocks containing quartz (silica) take an exceptionally long time to erode. However, silica sand is the primary type of sand that is used to make glass. That’s because it contains a high amount of silicon dioxide.
Silicate, also called silicon dioxide (SiO2), is the compound within glass that enables it to have many excellent properties. Some of these properties include:
- Low thermal expansion—has a low tendency to change its shape, volume, area, or density when temperature changes
- Resistance to thermal shock—can resist a sudden change in temperature that creates stress
- High temperature resistance—can typically withstand temperatures up to 1,832–2,732 °F)
- Resistant to chemical weathering—can withstand most acids
- Transparent—to visible light, ultraviolet, and infrared
Overall, sand is the primary material that is used to manufacture glass. Silica sand is the best type for making glass because it contains high quantities of silicon dioxide. This compound gives glass many of its great properties.
Soda ash (sodium carbonate)
Soda ash, also called sodium carbonate, soda lime, or washing soda (Na2CO3), is another compound added to glass. Pure soda ash is a white, water-soluble salt. Soda ash is added to glass because it lowers the melting temperature of silicon dioxide (the primary constituent of silica sand). Hence, soda ash is a flux—a substance that can reduce the melting point of another substance. A flux such as soda ash is required for making glass because the melting point of silica sand is exceptionally high at 3,110 °F. Therefore, it makes the manufacturing process more efficient by reducing the melting point of silica sand to 1,562 °F.
Limestone (calcium carbonate)
Limestone, also called calcium carbonate (CaCO3), is another compound added to glass. Pure limestone is a white powder that is poorly soluble in water. Limestone is added to glass because it helps stabilize glass. Thus, it increases the durability of glass to prevent it from breaking down.
Waste recycled glass
Glass is entirely recyclable and can be recycled indefinitely without compromising its quality. Because of this, new glass can be made from old glass. The process is relatively straightforward. All it requires is cleaning the glass, crushing it, and then remelting it to form a new product.
Additives
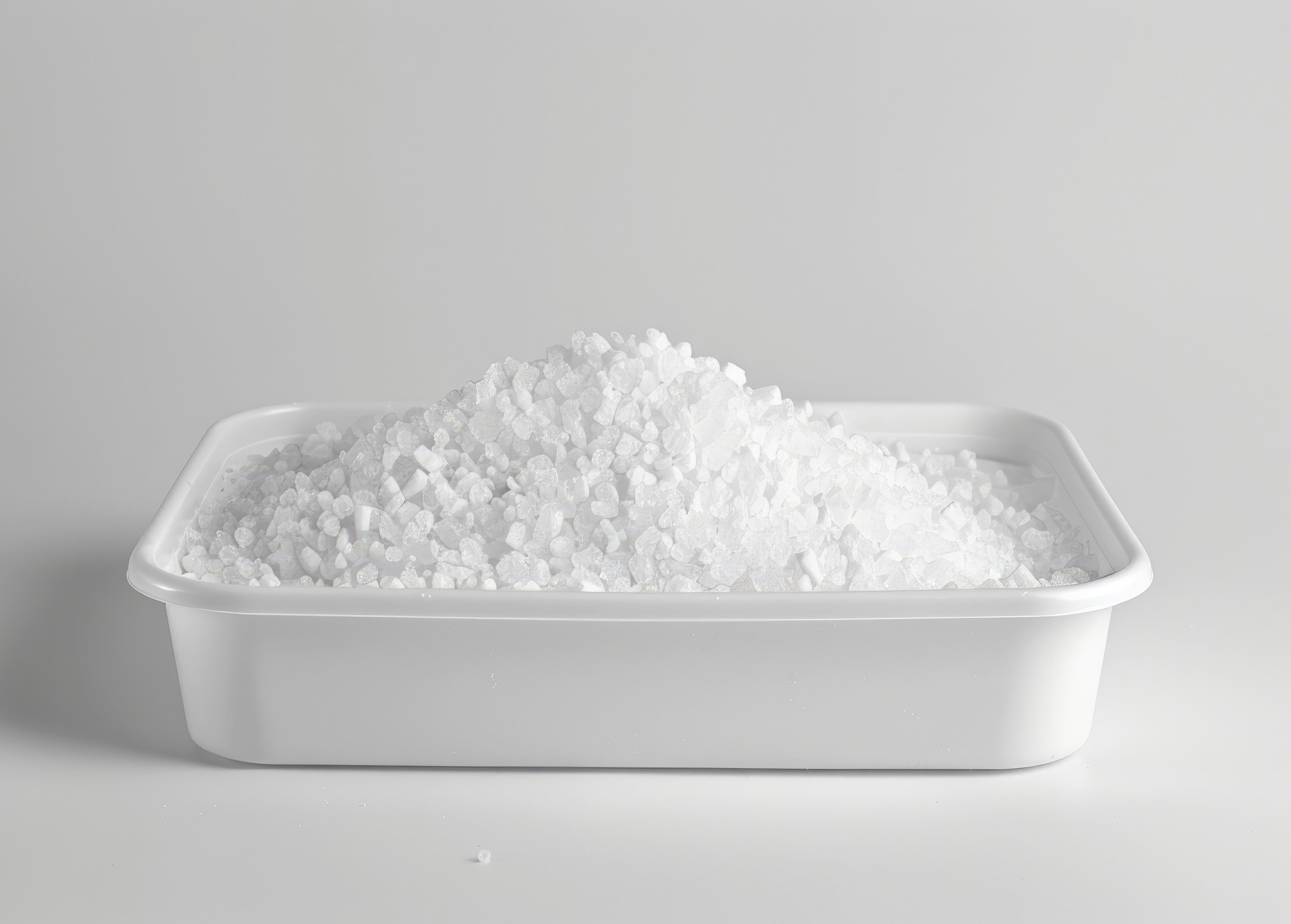
- Barium nitrate—makes glass clearer and prevents discolouration
- Barium oxide—can be used as a flux
- Iron—enables glass to absorb more heat and infrared energy
- Lanthanum oxide—increases the refractive index of glass
- Magnesium oxide—increases the stability of glass
- Sodium sulfate—prevents air bubbles from forming in the glass
03/AGC’s Flat Glass Manufacturing: Float Process
AGC’s float method can produce glass at the same level as the fusion method in the manufacture of cover glass for electronic applications. In addition, the float glass process is capable of producing large quantities of glass at one time due to the large scale of the furnace. Therefore, it can be said that the float method can produce glass at a lower unit cost than the fusion method in the production of cover glass for electronic applications. AGC has established the float method by applying advanced technology, which enables the above production.
The raw materials that AGC use for their float glass are:
- Silica
- Glass cullet
- Sodium carbonate
- Dolomite
- Limestone
- Sodium sulfate
- Iron oxide or metallic compounds (for coloring)
AGC’s float glass process involves mixing the raw materials, melting them in the furnace, and pouring the molten glass onto a bath of molten tin. As the glass floats on the tin bath, it solidifies. The glass ribbon then moves to an annealing zone, where it gradually cools while transported on rollers. Coatings can be applied to the glass after it sets.
AGC's Related Products
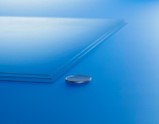
AS2: AGC's High Quality Float Glass for Various Applications
AGC's AS2 is a high-quality soda-lime glass produced by the float process, notable for its variety in thickness and high flatness, making it a glass of choice for a wide range of applications.
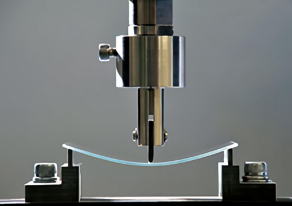
AGC Dragontrail™ Series: Aluminosilicate Glass
The Dragontrail™ series from AGC is an aluminosilicate glass suited for chemical strengthening. Compared to conventional glass or plastics, it possesses superior properties in strength, scratch resistance, and texture, making it ideal for use as durable and scratch-resistant cover glass.
04/FAQs
Is glass solid or liquid?
Glass is an amorphous solid. Other examples of amorphous solids are rubber and plastic. Solid materials can be defined as being either crystalline or amorphous. Crystalline solids consist of internal order. That means the atoms or particles are arranged in a specific order. In contrast, an amorphous solid lacks order because the atoms are arranged randomly. Sometimes, glass is classified as a supercooled liquid. As a result, this would imply that the atoms within glass are slowly moving. However, this description of glass is often deemed inaccurate or misleading because the atoms are not moving freely. Therefore, glass is an amorphous solid and not a supercooled liquid. Despite this, it’s important to note that even amorphous solids are still considered a state of matter that lies between a solid and liquid.
How was glass made historically?
Glass has been made for many centuries and is believed to have originated in Mesopotamia, most likely around 2,500 BCE. Ancient humans may have discovered glass by experimenting with sand when it was heated. The production of glass during ancient times was somewhat limited. However, the Roman Empire perfected glass-making by adding soda ash to the process. Glass-making became widespread, and many countries throughout Asia and Europe perfected the art. As a result, different additives were incorporated into the process to change the color of glass or improve its durability.
Because high temperatures are required to melt sand, furnaces were used since open fires did not provide enough heat. In addition, some furnaces were heated with coal instead of wood because coal releases more heat. Today, the process of making glass has expanded so that it can be manufactured in high volumes. Glass is also used for a wider variety of purposes, meaning the process has become more refined with different methods and additives.