Automotive display glass
- Introduction
- 1. Size
- 2. Shape
- 3. Functionality
- Low reflectivity (high visibility)
- Anti-reflection Treatment
- Safety (difficult to crack)
- Antifouling (difficult to get dirty)
- Antifouling treatment
- Aluminosilicate Glass
- Soda lime Glass
- Dragontrail™
- Dragontrail™ Pro
01/Advancements of Display Glass
Automotive displays are advancing year-by-year. As various features are added to them over time, they are becoming larger and more complex in shape. This is where the safety design of display cover glass is important. In this article the trends and required technologies for display cover glass are explained. AGC’s cover glass products are detailed at the end.
Introduction
The changes surrounding the auto industry, such as automated driving, electrification, and connected vehicles, are changing the nature of automotive displays. Year after year, the cover glass used in these displays is trending towards larger sizes, increasingly complex shapes, and an increase in functionality. At the same time, safety design is an obvious requirement.
1. Size
The world’s first GPS navigation/CCS unit introduced in 1990 included a display whose size was extremely small. The general display size of almost all commercially available navigation units of this area was 7 inches or less. The size of in-vehicle displays has trended larger annually ever since.
2. Shape
Automotive displays enable drivers to visually grasp a wealth of information. With the continued advances in automated driving, the shape of these displays will probably continue to increase in complexity. For example, the 10.1-inch curved display glass in the new Audi A8 is manufactured using 3D curved surface processing technology. As the display designs continue to diversify, so should the display shapes.
3. Functionality
Automotive displays employ more functionality than just touch panels. For example, there are technologies such as augmented reality heads-up displays (AR HUDs) that project road information directly onto the windshield. And in 2020, Continental developed a 3D display for use in automotive applications. As cars become more connected with mobile technology, displays are being used in a variety of ways.
02/Desired Quality and Technology
The requirements of glass are low reflectivity (high visibility), safety (difficult to crack), and antifouling (difficult to get dirty). What kinds of technologies might each of these employ?
Low reflectivity (high visibility)
Conventional sheet glass is said to have a visible reflectance of 8%. What that means is with that amount of reflectance, there is that much difficulty in recognizing objects on the opposite side of the glass. For glass to be useful in automotive applications, it is essential to reduce the visible light reflectance and increase the visibility.
Anti-reflection Treatment
Anti-reflective glass refers to glass with a special coating applied to both sides. In contrast to the 8% visible reflectance of float sheet glass, anti-reflective glass can reach a value under 1%.
The technology behind this anti-reflective glass can also be employed in the creation of automotive displays. Since sunlight shines from every which angle inside a vehicle, displays can become difficult to see properly due to all the reflections. To make them easier to see, the visible reflectance of the display cover glass must be as low as possible. While each manufacturer is researching anti-reflective technologies, and the world’s automobile windshield to employ anti-reflective glass (eXeview) was developed by AGC in the year 2000.
Safety (difficult to crack)
In order to maintain driver safety, glass must be resistant to impacts.
Chemical Strengthening Treatment
Chemical strengthening gives strength to the glass through a process of ion substitution. Basically, by substituting sodium ions in the glass with bigger potassium ions, a layer of compression is formed on its surface. To facilitate the transfer of the sodium and potassium ions, the substitution takes place while the glass is immersed in a potassium nitrate molten salt solution for a period of time at around 400℃.It varies by the different applications for the glass, but a compression layer between 10 and 100μ forms on both sides of the glass. Also, chemically strengthened glass differs from heat-strengthened glass in that the creation of a strong layer can be done for very thin sheets of glass, which is an advantage.
Antifouling (difficult to get dirty)
When glass is easily dirtied, it can become difficult to easily parse information, which can raise safety issues. There are methods to apply a coating called a photocatalyst to better defend against the glass being soiled.
Antifouling treatment
To create stain resistant glass, a material called a photocatalyst is used. A photocatalyst is a coating that consists mainly of titanium dioxide. When titanium dioxide is exposed to sunlight, an oxidative decomposition reaction occurs and contaminants are removed. The oxidative decomposition reaction weakens the absorption of impurities to the point that it can be washed away by rain. Through this mechanism, glass can remain clean for long periods of time.
03/Production method
A method of manufacturing glass to be used as automotive cover glass is the float glass process. The float glass process is a method of forming glass by molten glass being poured over molten tin. The process is as follows.
- The raw materials for the glass are melted in a kiln at a high temperature of around 1600℃.
- The molten glass is poured over a float bath filled with molten tin.
- After the glass is cooled in a slow-cooling furnace, it undergoes pulling to adjust its thickness.
- The hardened glass is cut to the desired size.
- The cut glass is inspected.
One of the advantages of the float glass process is that the price of glass manufactured this way can be kept down due to the fact that the production of great quantities of glass can be done at one time. In addition to that, the float glass process can also handle the manufacturing of glass in a wide range of thicknesses.
04/Materials
There are many types of glass used to produce automotive cover glass and each has its own characteristics. What follows are details about two of those types: aluminosilicate glass and soda lime glass.
Aluminosilicate Glass
Aluminosilicate glass is a glass that is comprised mainly of silica (SiO₂) and aluminum oxide (Al₂O₃). An advantage of this type is that is more scratch resistant than soda lime glass, and has superior impact resistance. It is mainly used for smartphone cover glass.
Soda lime Glass
Soda lime glass is a glass that is comprised mainly of silicon dioxide (SiO₂), soda ash (Na₂O), and lime (CaO). Since it can be manufactured so cheaply, it is used mainly for applications such as windows, bottles, and glass tableware. It is necessary to use it with caution because it is weak to sudden temperature changes.
05/AGC's Automotive Display Glass
AGC offers protective cover glass for electronic devices that boasts outstanding strength as well as scratch resistance. The advantages and differences of both types of glass products are explained in detail. In addition to the following two types of glass as Automotive Display Glass, we handle a variety of glass materials according to customer needs.
Dragontrail™
Dragontrail™ is a chemically strengthened special glass that was developed specifically to suit cover glass for smartphones, tablets, and other applications such as automotive displays. This glass has a flat shape, protected by a housing, and features resistance to cracks. Compared to conventional glass or plastics, it offers superior strength, abrasion resistance and touch feel. Dragontrail™ is highly valued for being easy of view and even easier to operate in navigation or other automotive information display panels, and is already employed in many vehicles.
Dragontrail™ Pro
Dragontrail™ Pro is a cover glass that achieves approximately 1.5x the strength of surface compression stress of Dragontrail™. The best feature of this glass is that it has the capability to be curved to fit the form factor of modern smartphones, while still being stronger than conventional products.
AGC’s Specialty Glass Solutions
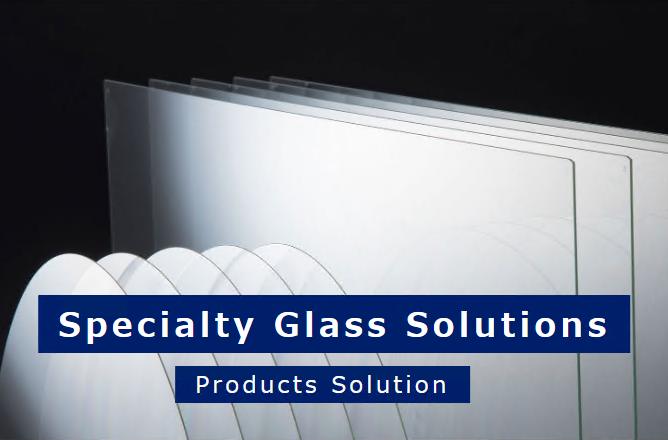
Specialty Glass Solutions
AGC's Specialty Glass Solutions offers unique solutions to customers' various issues related to specialty glass for electronic devices.