Glass as an Electronics Material
Glass, a transparent amorphous solid material, has a rich history rooted in precious materials. Over time, its applications expanded from household products, owing to its chemical stability and transparency. In the industrial age, it found use in lighting, architectural windows, and automotive windshields.
Today, glass plays a pivotal role in crafting windows and screens for electronic devices. This professional guide provides insights into the use of the different types of glass in electronics, including their properties and applications.
- Smartphone/Tablets
- Laptops
- Automotive Display
- Advanced Applications
- Robotics
- Telecommunication
- Space industry
- Mechanical Properties
- Hardness
- Tensile strength
- Compression resistance
- Thermal Properties
- Thermal resistance
- Thermal expansion
- Thermal conductivity
- Optical Properties
- Refractive index
- Absorption
- Reflection
- Chemical Properties
- Chemical resistance against water
- Chemical resistance against acid
- Electrical Properties
- Conductivity
- Permittivity
- Soda-Lime Glass
- Aluminosilicate Glass
- Non-alkali glass
- Fused quartz glass
- Borosilicate glass
- Glass ceramics
- What is glass?
- How is glass made?
01/Uses of Glass in Electronics Industry
In the electronics industry, glass emerges as a fundamental material, shaping the form and function of various devices. From smartphones to space exploration, the diverse applications of glass showcase its versatility and indispensable role in advancing technological frontiers. Explore the intricate connections between glass and electronics below.
Smartphone/Tablets

Laptops
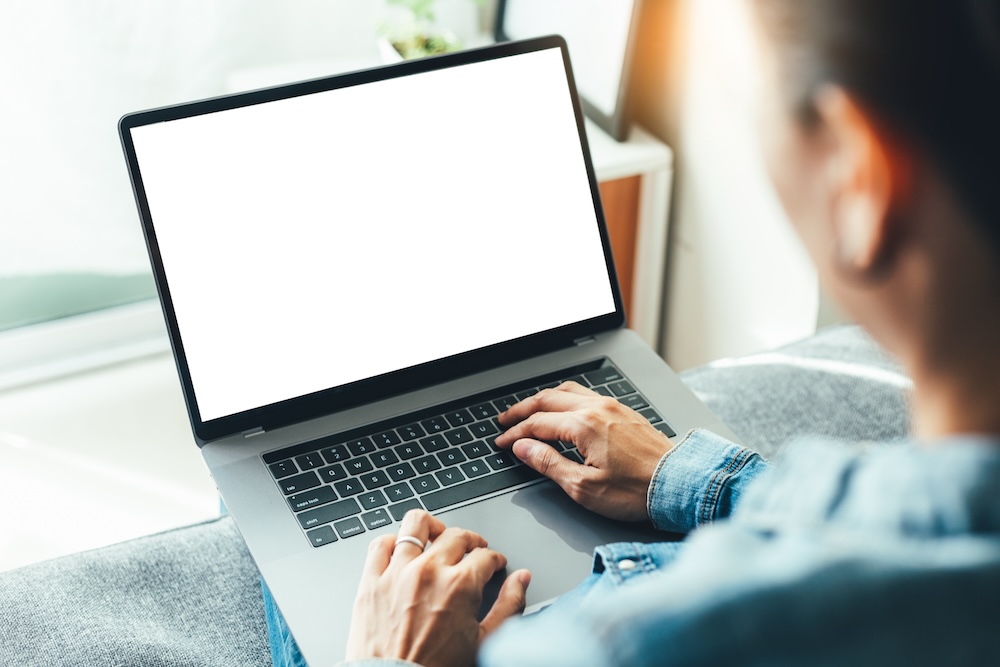
Automotive Display
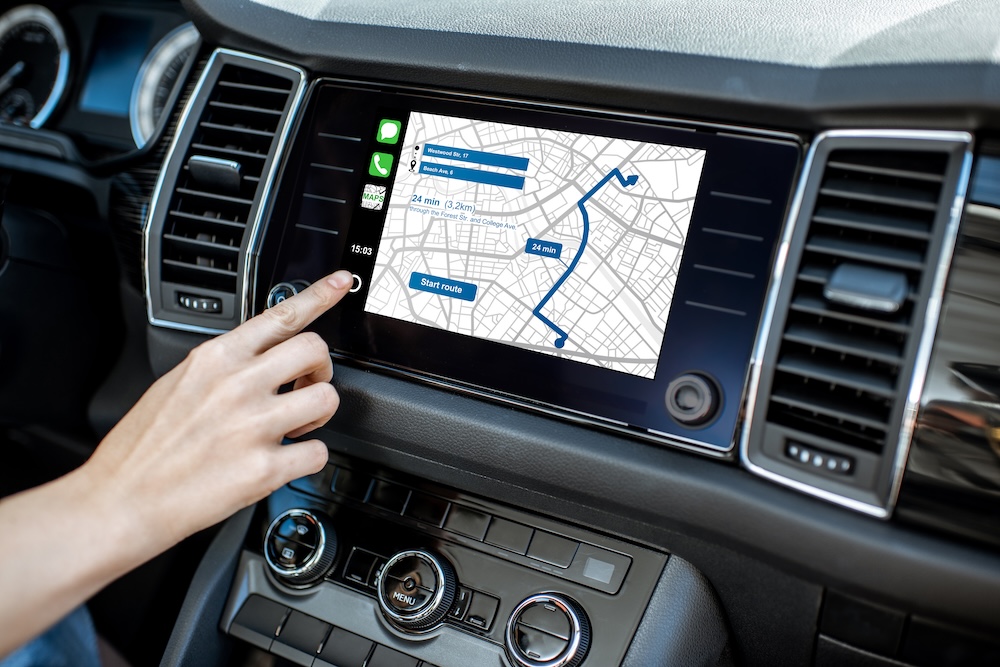
AGC's Related Products
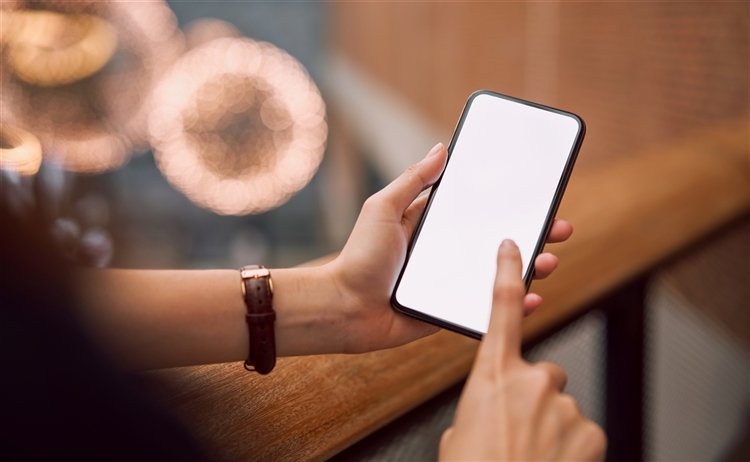
Smartphone Cover Glass
Cover glass is a component used for the exterior of smartphones. It must also meet the following six needs: Durability, Scratch resistance, Touch feel, Thinness, Transparency, and Flexibility.
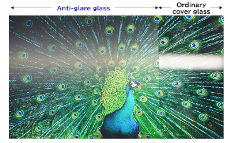
Anti-Glare Etched Glass
AGC's Anti-Glare Etched Glass is an innovative solution designed to mitigate the issue of glare on display panels, enhancing visibility and functionality.
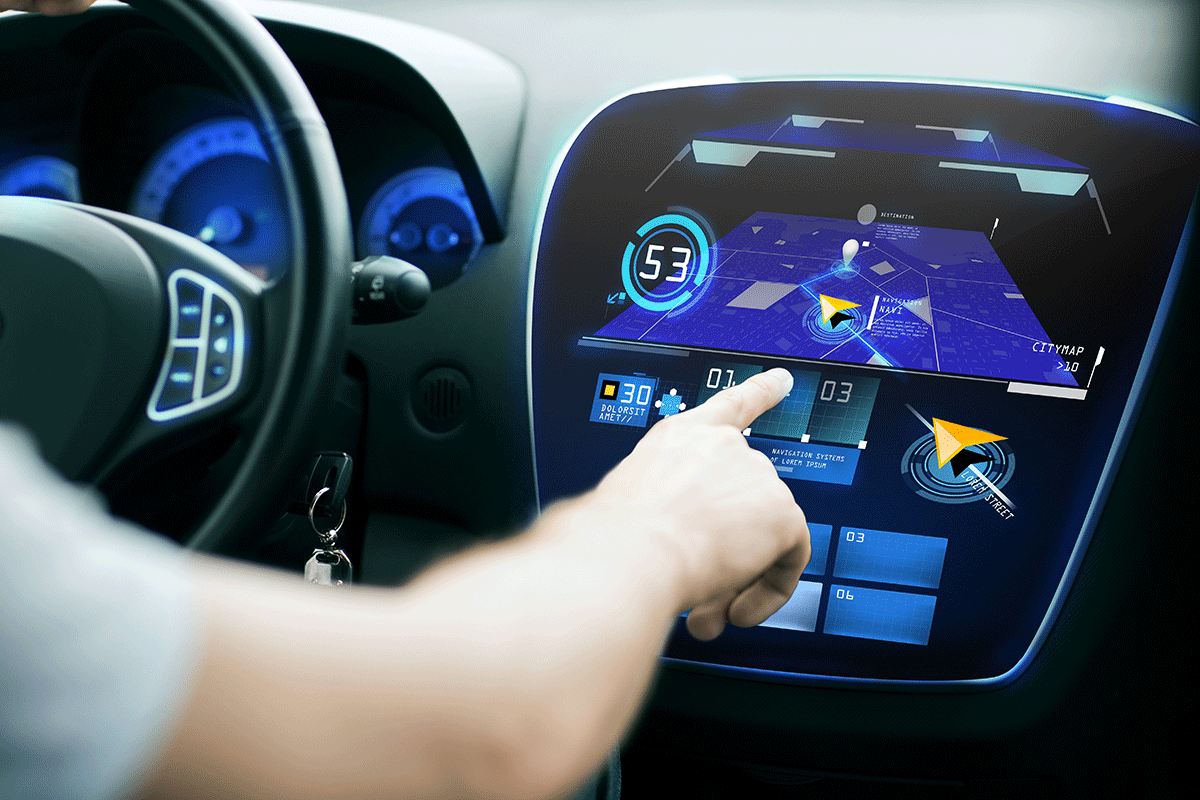
Automotive Display Glass
Automotive Display Glass is becoming larger, more complex, and more functional every year. The elements required of glass are "low reflectivity," "safety," and "antifouling". This article introduces three technologies to meet these requirements.
Advanced Applications
Glass plays a vital role in the forefront of the electronics industry. Here, we will introduce some examples of its applications.
Robotics

Glass finds applications in robotics, serving as a protective cover for cameras and sensors mounted on robots. The use of glass ensures clarity and protection, crucial for the optimal functioning of these advanced machines.
Telecommunication
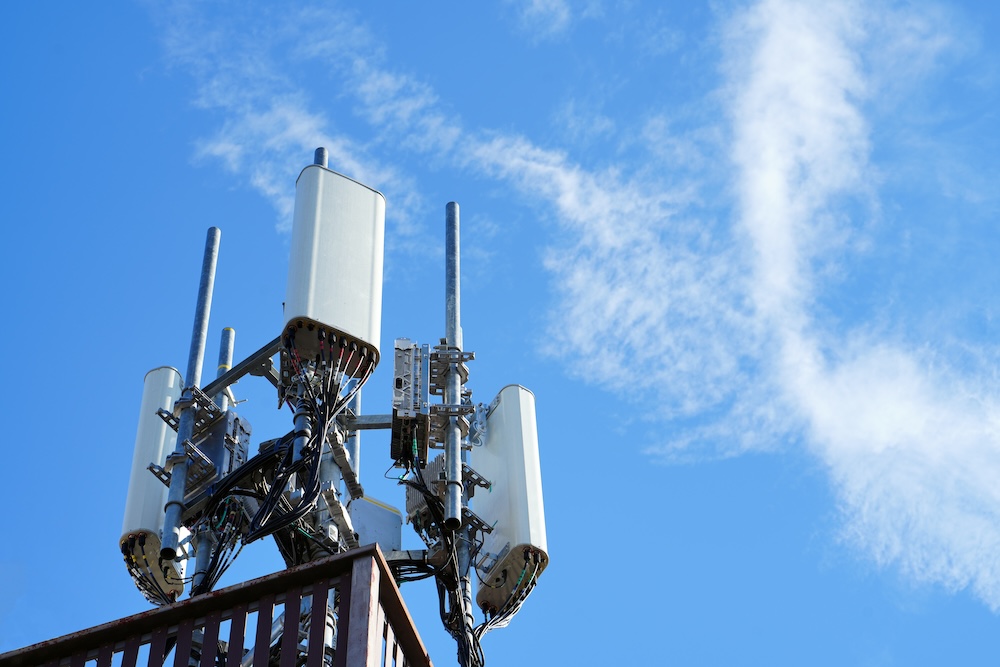
In the dynamic realm of telecommunications, glass finds its application as substrates in antenna systems for next-generation communications, particularly 5G. The unique attributes of glass, such as its durability and signal transparency, render it an ideal choice for enhancing and supporting the infrastructure of advanced communication technologies like 5G.
Space industry
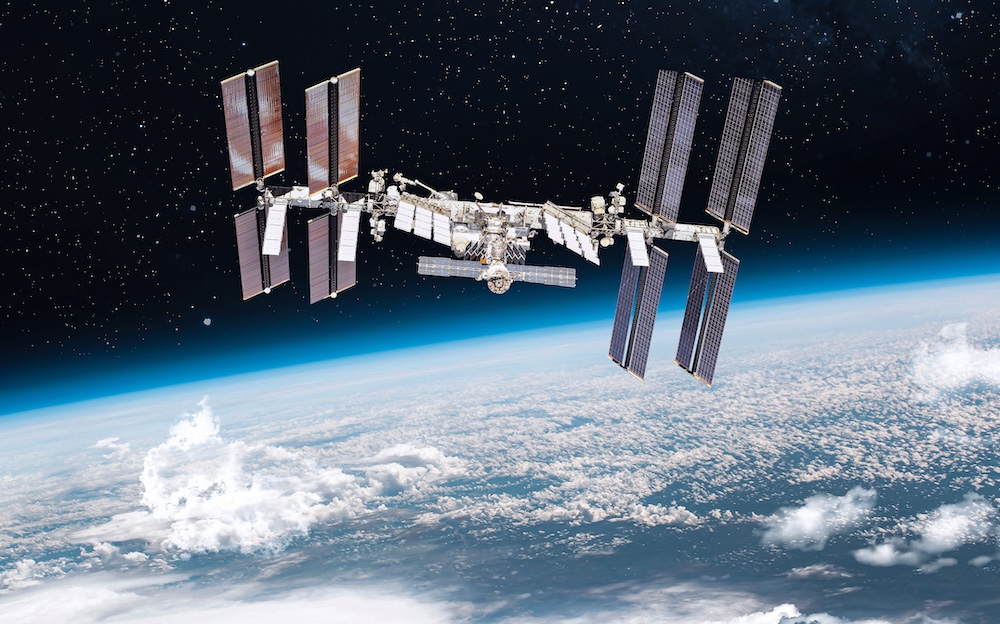
Glass takes its place in the vastness of space, being utilized in space satellites and stations (spacecraft). Its durability and optical properties make it an essential material for applications like space exploration and satellite communication.
Contact AGC if you are considering using glass in next-generation applications.
Connect with
AGC Today
02/Glass Properties for the Use of Electronic Devices
Explore the distinctive properties of glass that position it as a pivotal material in the electronics industry. Glass, with its unparalleled transparency, heat resistance, and unique mechanical, thermal, optical, chemical, and electrical attributes, undergoes a transformative journey to meet the stringent demands of electronic applications.
Mechanical Properties
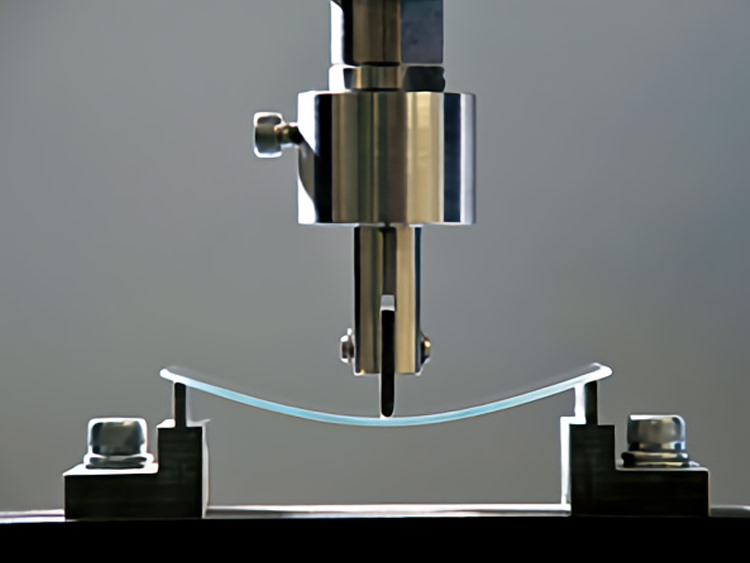
Hardness
Glass hardness, measured at 470 HK under the Knoop hardness test, ensures resistance to scratching, guaranteeing durability in electronic displays and surfaces.
Tensile strength
Tensile strength at 70,000 MPa fortifies glass against breaking, contributing to the structural foundation of electronic devices. This resilience ensures the longevity of glass components in the dynamic electronic environment.
Compression resistance
With a compression resistance of 800–1,000 MPa, glass stands resilient, shaping the stability of electronic components. This property is crucial for withstanding external pressures and ensuring the structural soundness of delicate electronic parts.
Thermal Properties
Glass's response to heat is a critical consideration in electronics, influencing its ability to endure and perform under varying temperature conditions.
Thermal resistance
High thermal resistance determines glass's capacity to endure elevated temperatures in electronic applications. This property is essential for preventing thermal damage and maintaining the functionality of electronic devices.
Thermal expansion
Glass exhibits a thermal expansion rate of 9.10–6 K-1, navigating temperature changes in electronic devices. This characteristic ensures that glass components can adapt to temperature fluctuations without compromising structural integrity.
Thermal conductivity
With a thermal conductivity of 0.8 W/mK, glass ensures stability in the intricate dance of temperature fluctuations. Efficient thermal conductivity is vital for preventing overheating and ensuring the optimal performance of electronic systems.
Optical Properties
In the electronic realm, glass's optical properties dictate its interaction with light, influencing the clarity and visibility of electronic displays.
Refractive index
A refractive index of 1.52 showcases glass's bending capability, crucial for lenses and prisms. This property is fundamental for the optical performance of electronic devices and precision in light transmission.
Absorption
Glass exhibits minimal light absorption (2-4%), ensuring optimal visibility in electronic displays. Low absorption is essential for maintaining vibrant and clear visuals on electronic screens.
Reflection
Controlled reflection (4%) enhances visibility, contributing to the clarity of electronic screens. This controlled reflection minimizes glare and improves the overall user experience with electronic devices.
Chemical Properties
Electronic devices demand resilience, and glass delivers high chemical resistance, safeguarding against environmental factors.
Chemical resistance against water
Glass resists water corrosion, making it ideal for containing or protecting against water in electronic applications. This chemical resistance ensures the longevity and reliability of glass components in the presence of moisture.
Chemical resistance against acid
While generally resistant, glass has limited resistance against specific acids, emphasizing careful selection for electronic components. This selectivity ensures the compatibility of glass with various environments, contributing to the durability of electronic devices.
Electrical Properties
Within the intricate symphony of electronics, glass takes center stage as a crucial insulator, providing a shield against unwanted electrical currents.
Conductivity
Glass, with its inherently low electrical conductivity, stands as a stalwart guard, preventing the flow of unwanted electrical currents in electronic devices. This property ensures the efficiency and reliability of electronic systems, where precise control over electrical flow is paramount.
Permittivity
Characterized by low permittivity, glass minimally stores electrical energy. This property contributes to the insulation of electrical components, ensuring the stability and functionality of electronic systems by reducing the risk of electrical interference.
03/Types of Glass Materials Used In Electronics
Soda-Lime Glass
Soda-lime glass, a versatile material widely acknowledged for everyday items like window panes, bottles, and bakeware, takes on a transformative role in the realm of electronics. Its adaptable nature finds expression as a key component in TN/STN LCD Panels, touch panels/cover glass for electronic devices, and mirror substrates. Comprising 70% silicon dioxide, 15% soda (sodium oxide), and 9% lime (calcium oxide), soda-lime glass proves its significance in enhancing the functionality and durability of electronic devices.
AGC's Related Products
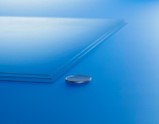
AS2: AGC's High Quality Float Glass for Various Applications
AGC's AS2 is a high-quality soda-lime glass produced by the float process, notable for its variety in thickness and high flatness, making it a glass of choice for a wide range of applications.
Aluminosilicate Glass
Aluminosilicate glass, known for its outstanding heat resistance and its capability to achieve high strength through chemical toughening, comprises a composition of 57% silicon dioxide, 20.5% alumina, 12% magnesia, 5.5% lime (calcium oxide), 4% boric oxide, and 1% soda (sodium oxide). This makes it a popular choice as a cover glass for electronic devices such as smartphones, tablets, and laptops. Its capability to endure higher temperatures compared to regular soda-lime glass ensures it's a dependable protector for sensitive electronic components.
Non-alkali glass
Non-alkali or alkali-free glass is used for FPD like LCD or OLED (Organic Light-Emitting Diode) displays. Therefore, it enhances the resolution like smartphones. Non-alkali glass can also be very thin while having minimal deformation. As a result, this type of glass, though very thin, is considerably resistant to damage. Non-alkali glass contains a range of compounds, mainly silicon dioxide, aluminum oxide, and boron trioxide. Depending on how it’s made, it may also contain small amounts of magnesium oxide, lime (calcium oxide), barium oxide, strontium oxide, or zinc oxide.
Fused quartz glass
Fused quartz glass is considerably different from commercial types of glass. That’s because it contains pure silica and doesn’t contain other compounds like commercial glass does. Because of this, it’s sometimes referred to as pure glass. Therefore, fused quartz glass has some unique properties. For example, it has a higher chemical and thermal resistance and increased transparency when compared to commercial glass. Fused quartz glass has a range of applications. Due to its high transparency, it’s primarily used for transmitting ultraviolet light. However, this glass can also be used for laser technology, electronics, and high-temperature operations.
Borosilicate glass
Borosilicate glass is made from silicon dioxide and boron trioxide. It’s widely used for laboratory glassware because it has good thermal and chemical resistance. Therefore, it’s ideal for scientific experiments that require heat or the use of harsh chemicals.
Glass ceramics
Glass ceramics combine the properties of glass with ceramics. Therefore, this material is a cross between glass and ceramics. The resulting material is highly crystalline. Depending on how it’s made, glass ceramics can be transparent or opaque. Other properties include lower thermal expansion, increased hardness, and higher resistance to thermal shock compared to commercial glass. Glass ceramics are commonly used for cooking purposes, such as cooktops, cooking appliances, grills, and barbeques. Most types contain lithium, aluminum, and silicon oxides. They may also include smaller quantities of sodium oxide, potassium oxide, magnesium oxide, or lime (calcium oxide).
04/Glass Related Q&As
-
What is glass?
-
Glass is a transparent amorphous solid material with various applications. Historically the origin of glass was very precious materials. Then the application expanded to household products as its chemical stability and transparency. In the industrial age, the glass used for lighting, architecture windows, automotive windshields etc. In the electronics age, it’s used to make windows or screens for electronic devices. While it’s a commonly used material, many people are unaware of where it comes from or how it is made.
-
How is glass made?
-
Glass is made by heating raw materials at very high temperatures. Modern industries are using the same process in 2000 years ago. These temperatures are typically 1700°C (3090°F) or higher, and at this temperature. the raw materials melt into liquid state and mixed into new compositions. During the cooling process, the melted glass is frozen into solid with new “glass” compositions. The resulting structure has an amorphous solid (having no apparent crystalline atomic structure) . Learn more about glass manufacturing process