Smartphone Cover Glass
- The Size of the Current Market
- Predictions for the Future of the Market
- Durability (Impact resistance from falls)
- Scratch resistance
- Touch feel
- Thinness
- Transparency
- Flexibility
- Fusion glass process
- Chemical Strengthening of Mother Glass
- Glass material composition
- Aluminosilicate Glass
- Soda-lime Glass
- Lithium Aluminosilicate Glass
- Glass Ceramics
- Dragontrail™
- Dragontrail™ Pro
- Dragontrail™ STAR Series
01/Smartphone Cover Glass Market
Smartphone cover glass is used on the exterior of smartphones. They protect the display screen or rear panel of the phone.
What follows is a description of the current state and future predictions of the market for cover glass, an absolutely essential smartphone component.
The Size of the Current Market
According to Proficient MarketInsights, the size of the smartphone cover glass market is estimated to have surpassed US$1.46 billion in 2021.
Up until 2017, the market for cover glass had grown along with the increase in smartphone units shipped. From 2017 and onwards, the number of phones shipped slipped into a decline, whereas the demand for the total area of cover glass continued to increase.
One of the factors for the increase in demand for the total amount of cover glass is the increase in smartphone size.
At present, the demand for cover glass for smart watches such as the Apple Watch, as well as for automotive displays, has continued to increase.
Predictions for the Future of the Market
According to DataM Intelligence, the average annual growth rate of smartphone cover glass between 2022 to 2029 will be 18.57% and is predicted to remain at an elevated level for the foreseeable future.
In the smartphone market, the proliferation of 5G communication from 2022 onwards is anticipated to result in demand for replacement smartphone units, and in 2024, it is expected that the total number of units shipped will eclipse previous records to reach 1.51 billion units.
In addition, steady growth is expected to continue in markets that are adjacent to smartphone cover glass, such as for smart watches and automotive displays.
02/6 Required Features of Smartphone Cover Glass
Cover glass is not only required to protect smartphones, it also must meet the needs of portability, comfort and design.
In order for cover glass to fulfill the above-mentioned roles, the following characteristics are required.
- Durability
- Scratch resistance
- Touch feel
- Thinness
- Transparency
- Flexibility
They will be explained in detail.
Durability (Impact resistance from falls)
Exterior cover glass must be durable. If the cover glass were to be damaged, smartphone features could be greatly compromised and it would be necessary to have the unit replaced.
The leading cause of impact damage to the exterior of a smartphone is due to accidental falls. What’s more, according to surveys, cracks caused by falls are the number one complaint that users have about cover glass.
Consequently, cover glass must have a high strength and be able to resist impact damage when a fall happens.
Abrasion resistance
Cover glass must be abrasion resistant (difficult to scratch) to keep the screen easy to view.
That’s because if the screen were to become scratched up to the point of not being able to view it properly, the experience of browsing websites or watching videos will become stressful.
Therefore, glass that is abrasion resistant with a high surface hardness is a requirement.
Touch feel
The smoothness one feels when touching cover glass is an important characteristic that enhances smartphone operability.
While individual preferences vary, cover glass with a touch feel that is neither too slippery nor too rough makes smartphones comfortable to use.
At AGC, research into the touch and feel of glass is carried out and surface profiles are manipulated so as to reproduce a pleasant tactile feel.
Thinness
Cover glass must be as thin as possible.
Since smartphones employ high-capacity batteries, in order to keep the phones as thin as possible, the cover glass is required to be thin. To keep the phones light in weight with ever increasing battery volume and capacity, there is no avoiding the fact that the other parts of the phone aside from the battery must be thin and light.
Consequently, a thin profile is one important characteristic for cover glass to have.
That being said, there is a trade-off between thinness and crack resistance. In order to be both thin and crack resistant at the same time, the strength of the glass itself must be enhanced.
It just so happens that AGC has succeeded in developing a special glass that has 4 times the strength of conventionally manufactured glass, and has succeeded in making thin cover glass as a result.
Transparency
In order to let users appreciate the true beauty of the display screen, cover glass must have a level of high transparency.
In order to realize that high level of transparency, it is necessary to minimize the impurities inside the glass, and to prevent both the absorption and scattering of light.
Only an advanced level of technology is capable of manufacturing cover glass that is both low in impurities and high in strength.
AGC has a system in place to cultivate an efficiently high level of material design by concentrating on fundamental research and leveraging a large volume of data.
Flexibility
As smartphone ownership has become the norm, not only functionality, but also design and comfortable feel have become important considerations.
Rounded shapes have become especially important to enhance the design.
It is for this reason why cover glass must be able to flexibly bend with a high level of flexural strength.
03/How is Smartphone Cover Glass Made?
One of the manufacturing methods for smartphone cover glass is what is called the “Fusion glass process” and one of the ways to strengthen the cover glass is through the process of “chemical strengthening”.
Additionally, to create cover glass with an exceptionally high level of strength, it is necessary to consider not just the manufacturing method, but also the material composition of the glass.
They will each be explained in detail.
Fusion glass process
The fusion glass process is a manufacturing process in which molten glass is made to float over tin metal, where it cools as it spreads out into a level, flat shape.
Glass is formed in a continuous manufacturing process through the following list of steps, from the input of raw materials, to the final cutting into desired shapes.
- Raw materials are put into a melting tank at a high temperature.
- Molten glass is poured onto a float bath at a regulated rate of flow.
- The glass that is pulled out begins to anneal in a controlled cooling tank.
- The annealed glass is cut into predetermined sizes.
- The cut glass undergoes inspections.
Because it is suitable to manufacture large quantities of glass, AGC employs the fusion glass process manufacturing method to mass produce functional, high-quality cover glass.
It is for that reason that AGC is able to proudly contribute to the spread of smartphones to even more users while achieving a lower cost of production.
How is glass made "Float glass process"
Chemical Strengthening of Mother Glass
To achieve the high strength required of cover glass, the glass must be treated by a process called chemical strengthening to create a layer of high compression on its surface.
A thin layer of compression of about 10-100 microns is formed by replacing sodium ions in the surface of the glass with potassium ions.
The chemical ion exchange is caused by immersing the mother glass into a strengthening solution heated to around 400°C for a period of time.
An important consideration for creating high strength glass through chemical strengthening is the material composition.
Using a different material composition could bring about greatly varied results even if treated with the exact same process.
Therefore, AGC puts a considerable amount of effort into fundamental research to enhance its material design capabilities to develop its high strength cover glass.
Glass Material Composition
Glass material compositions and their suitable applications are explained in detail.
Aluminosilicate Glass
Aluminosilicate glass is a commonly used material in which the main constituents are silica (SiO₂) aluminum oxide (Al₂O₃), and can include sodium oxide (Na₂O). Its composition was developed to be suitable for chemical strengthening.
Applications for chemically strengthened aluminosilicate glass include pressure-resistant watches, cover glass for smartphones, and in recent years this list has expanded to include automotive displays.
Soda-lime Glass
Soda-lime glass consists mainly of silicon dioxide (SiO₂), soda ash (Na₂O), lime (CaO).
It is the most commonly used glass for residential and automotive applications as it is the most cost effective.
Lithium Aluminosilicate Glass
Lithium aluminosilicate glass is a material that differs from aluminosilicate glass in that the lithium (LiO₂) is used instead of sodium oxide (Na₂O).
An advantage of using lithium (Li) ions, which have a higher diffusion rate than sodium (Na) ions, is that this allows the compression layer to be deeper.
Lithium aluminosilicate glass is mainly used for cover glass for smartphones and tablets.
Glass Ceramics
A glass ceramic is a material created by adding certain additives to the materials used to create normal glass, shaping it, and then reheating it, causing crystals to form inside.
The crystals inside the glass impart the characteristics of being high in strength and resistant to thermal expansion.
As a consequence, applications include super heat-resistant tableware, as well as fireproof and fire-resistant building materials.
04/AGC Smartphone Cover Glass
The following smartphone cover glass products are developed and supplied by AGC.
Dragontrail™
Dragontrail™ is a special chemically strengthened cover glass that developed specifically for smartphones and tablet PCs.
Compared to conventional glass and plastics, it is stronger, more abrasion resistant and offers superior texture.
Dragontrail™ boasts environmentally friendliness as a feature, as no lead, arsenic, nor antimony are used in the manufacturing process.
Dragontrail™ Pro
Dragontrail™ Pro takes the surface compressive stress of Dragontrail™ even further resulting in being about 1.5 times stronger.
This means that curved surfaces can be made stronger, making the glass more resistant to edge cracking.
Dragontrail™ Pro is ideal for applications such as smartphones with curved edge displays.
Dragontrail™ STAR series
Dragontrail™ STAR series is a cover glass that boasts 4 times the strength of the original generation of Dragontrail™.
The enhanced strength lets us achieve cover glass that is even thinner than Dragontrail™ Pro.
As a result, this enables a high degree of added value being bendable and low in weight, meaning it can be used for not only display screens, but also for the protection of rear covers.
AGC’s Specialty Glass Solutions
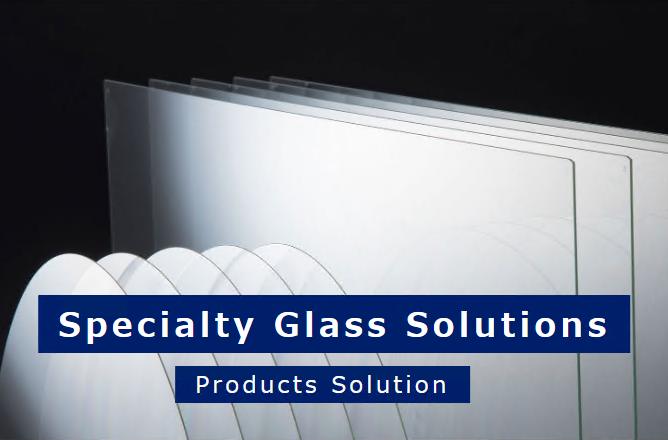
Specialty Glass Solutions
AGC's Specialty Glass Solutions offers unique solutions to customers' various issues related to specialty glass for electronic devices.